Understanding the ratio between cost and performance is critical when building an EMI shielded container for a circuit board. So far, a lead-lined cabinet is the best for protecting your stuff from radiation. From an electromagnetism compatibility (EMC) standpoint, the material used will directly impact project price and application performance. NuclearShields. has a wide range of materials to suit the requirements of any needs, from pre-tin coated steel to highly permeable metal. Our Application Engineers are experienced and eager to help you get started. RFI Shielding Popular MetalsPre-tin plated steel in both shiny and matte finishes and copper alloy 770, often known as nickel silver or German silver, are the most popular metals utilized by Leader Tech clients for RFI / EMI shielding. Here’s a short rundown of how they each work: #1 Steel with a Pre-Tin CoatPre-tin plated steel is a low-cost thing that works well from kHz to lower GHz frequencies. Carbon steel has a low-frequency magnetic shielding characteristic that alloy 770, copper, and aluminium lack. The tin coating protects the steel from corrosion and provides an excellent solderable surface for attaching the shield to the wires on the top board during assembly. #2 Nickel Silver Copper Alloy 770Copper alloy 770, sometimes known as alloy 770, is a corrosion-resistant copper, nickel, and zinc alloy used in EMI shielding applications. UNS C77000 is the alloy’s designation in the unified numbering system. The base material is attractive and does not need to be post-plated to become corrosion-resistant or solderable. Beginning in the mid-kHz range and up to GHz, the material performs effectively as an EMI shield. The permeability is 1, making it suitable for MRI applications that don’t allow magnetic materials. #3 CopperBecause it is highly efficient at attenuating magnetoelectric waves, copper is the most dependable metal for EMI shielding. Copper is used in RFI shielding in many applications, from hospital MRI machines to simple computer equipment. This metal and its alloys brass, phosphoric bronze, and beryllium copper can be readily manufactured due to its flexibility. These metals are more expensive than pre-tin coated steel or copper alloy 770 shielding alloys, but they have more excellent conductivity. Because of their flexibility, phosphorus bronze and beryl copper are more frequently utilized in battery or spring contact applications. #4 AluminiumBecause of its non-ferrous characteristics, strength-to-weight ratio, and high conductivity, aluminum is a good option for various applications. While compared to copper, aluminum has approximately 60% conductivity; nevertheless, its galvanic oxidation and corrosion characteristics must be carefully considered when utilizing this metal. On its own, the material will oxidize and has poor solderability. |
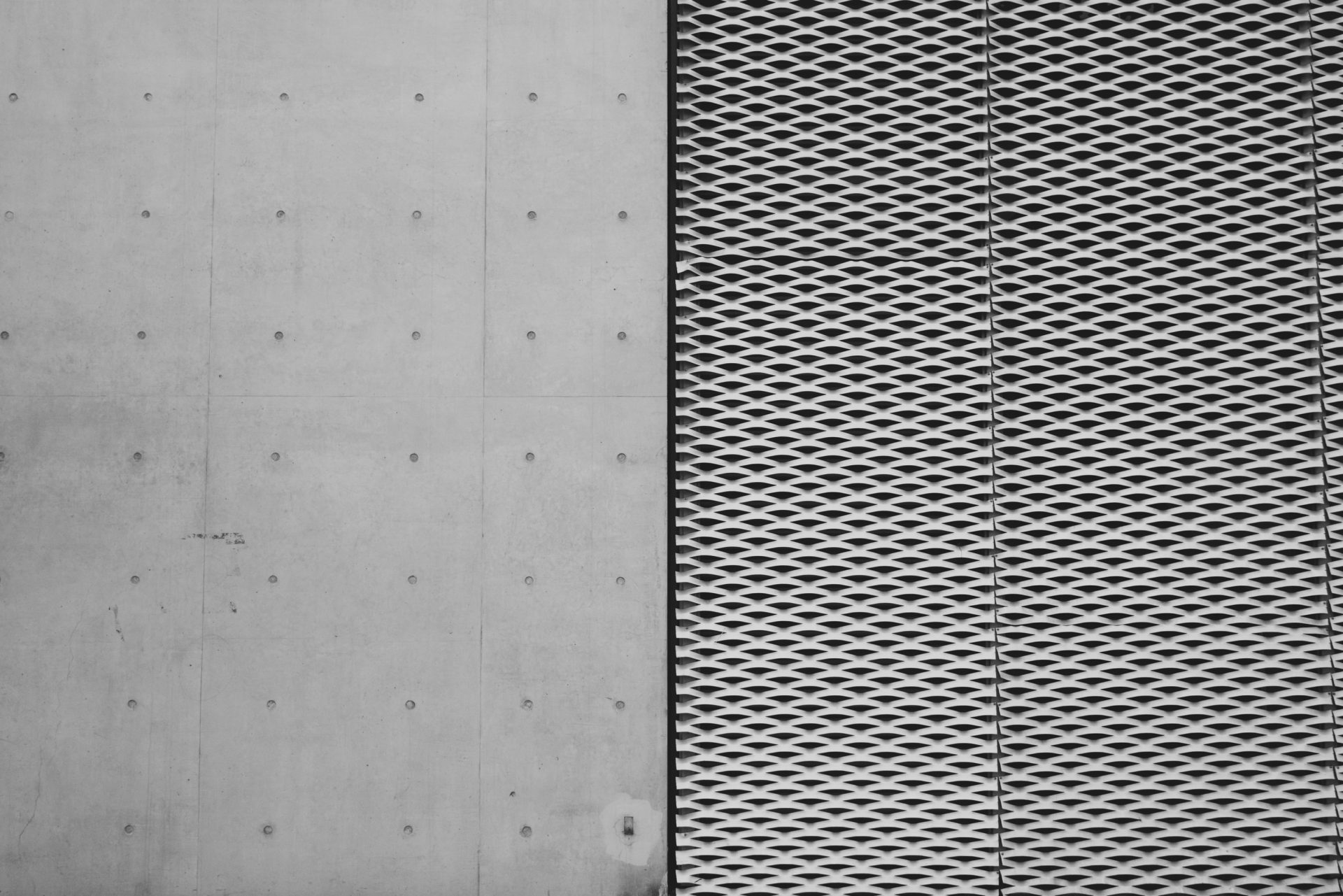